3RRL
Administrator
Huge Kama
Posts: 2,027
|
Post by 3RRL on Jun 8, 2008 14:26:56 GMT -5
Oh man Larry, that is going to be one heck of a rake. You must have a gazzilion bucks in it by now with all that steel, those bearings, cylinders and heavy duty hardware. It will be the best one on the planet, I'm sure. Why do you need to bend steel for the 3pt "A" frame? Can't you fabricate one from square tubing and weld it together? If you already have the steel stock, consider sawing an welding instead? Rob-
|
|
|
Post by bradblazer on Jun 8, 2008 22:45:50 GMT -5
I bent some 1x1" stock for my toothbar on my little 12 ton shop press. To get 45 deg. you mignt need to do something to keep the side supports from sliding out. I also bent some 1/4 x 6" plate by putting a piece of 3/4 x 2" stock on edge under the press foot.  
|
|
GuglioLS
Administrator
Jinma354 LE
Posts: 1,276
|
Post by GuglioLS on Jun 8, 2008 23:49:49 GMT -5
Rob, Thanks for the generous compliments. As far as cost go, it's not that bad, I only had to buy about 75 in new steel, the plasma cut steel was bartered for my time to repair an antique 3 phase 250 amp MIG. Rake tines were 125, cylinders and flange bearings came to 200. Nuts, bolts and miscellaneous hardware I get from that Surplus City place in Albuquerque for 2 bucks a pound. Remember that place? As far as bending flat bar, Isn't bent flat bar stronger than cut and welded? Plus I think bent steel (as long as it's bent in the right direction) looks better, to me anyway. And I have that 20 ton press I want to put it to good use. Brad, Thanks for the metal bending pics, tips and tricks, I got some ideas from Renze over on TBN as well. Man your tooth bar is super heavy duty. I did not make any progress on the rake today, BUT I did make an Anvil and Die as suggested by Renze for my hydraulic press. I spent all day on that. I've been wanting to make an anvil for the press so this rake project was just as good an excuse as any. Here goes the anvil and die project to bend steel for the TPH triangle mount.... Took a chunk of 3" dia round bar x 3" long, trued the ends, drilled a 1/4" hole clean through, then drilled a 1.5" dia hole 1.25" deep. 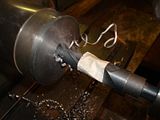 Larry
|
|
GuglioLS
Administrator
Jinma354 LE
Posts: 1,276
|
Post by GuglioLS on Jun 9, 2008 0:02:40 GMT -5
|
|
GuglioLS
Administrator
Jinma354 LE
Posts: 1,276
|
Post by GuglioLS on Jun 9, 2008 0:12:27 GMT -5
|
|
GuglioLS
Administrator
Jinma354 LE
Posts: 1,276
|
Post by GuglioLS on Jun 9, 2008 0:39:53 GMT -5
|
|
GuglioLS
Administrator
Jinma354 LE
Posts: 1,276
|
Post by GuglioLS on Jun 9, 2008 0:55:22 GMT -5
|
|
GuglioLS
Administrator
Jinma354 LE
Posts: 1,276
|
Post by GuglioLS on Jun 9, 2008 1:06:46 GMT -5
Oh boy here we go............. 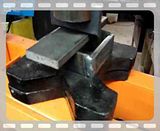 Well it works better than expected. At least I'm impressed. I got a little over 45* so some sort of a stop at the bottom of the die should allow for more precise bends. Thank's to Renze for the idea of using C channel to make a die. The anvil is not too shabby either. Check out the close up's of the bend..... 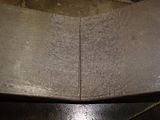 With this setup I should be able to accurately bend up to 1/2 thick by 3" wide flat bar for the TPH mount on the Rake project. Maybe I'll get to that by mid week? Larry
|
|
quikduk
CTW Life Member
 
Dog House
Posts: 552
|
Post by quikduk on Jun 9, 2008 10:12:25 GMT -5
Totally cool Larry  and a stunning job as usual!!!
|
|
GuglioLS
Administrator
Jinma354 LE
Posts: 1,276
|
Post by GuglioLS on Jun 9, 2008 10:53:07 GMT -5
Thank you Duk, Here is a pic of the TPH mounting arms, not sure what the correct technical term for those two pieces are. In any-event those are what needs to be bent on the press. Does the geometry look correct for a TPH? 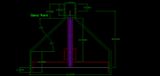 Larry
|
|
3RRL
Administrator
Huge Kama
Posts: 2,027
|
Post by 3RRL on Jun 9, 2008 11:13:37 GMT -5
Wow, very cool Larry. A lot of work for the anvil and die, but they sure work great. That crazy Dutchman must know his stuff! hahaha. The geometry looks good to me, but you can check it with the Standards of 3pt hitch categories, but I'm sure you've already done that. Great stuff Larry! Rob-
|
|
red
CTW Advanced Member

Posts: 306
|
Post by red on Jun 9, 2008 11:36:50 GMT -5
Wow, very cool Larry. A lot of work for the anvil and die, but they sure work great. That crazy Dutchman must know his stuff! hahaha. Rob- My wife's part Dutch. . . . that explains a lot... Rob you're part Dutch too ? (that explains a WHOLE lot ha haha! ;D) Super Job Larry! I read Renze post on the other site and now understand what he was talking about. Thanks for sharing -Ed
|
|
3RRL
Administrator
Huge Kama
Posts: 2,027
|
Post by 3RRL on Jun 9, 2008 12:08:59 GMT -5
|
|
GuglioLS
Administrator
Jinma354 LE
Posts: 1,276
|
Post by GuglioLS on Jun 9, 2008 13:09:44 GMT -5
Wow, very cool Larry. A lot of work for the anvil and die, but they sure work great. That crazy Dutchman must know his stuff! hahaha. Rob- My wife's part Dutch. . . . that explains a lot... Rob you're part Dutch too ? (that explains a WHOLE lot ha haha! ;D) Super Job Larry! I read Renze post on the other site and now understand what he was talking about. Thanks for sharing -Ed Thanks Ed. Yea all those crazy Dutchmen look and act alike. Does your wife know about machining and metal bending? Must be something in the water or the effect of wearing those wooden shoes. I sometimes wonder if that little dutch boy ever got his finger out of the Dyke? Larry
|
|
quikduk
CTW Life Member
 
Dog House
Posts: 552
|
Post by quikduk on Jun 9, 2008 13:53:20 GMT -5
Yeah, he did...but only because he had another Dutch friend machine him an oversized plug for it... ;D
I think your geometry looks right. I believe the centerline dimension from lift arm pin to top link pin is either 18" or 18.5". Check your box scraper and back blade and see what they are JIC.
I would think you might want some flat triangular plates for gussets at the lower angles (inside of the frame) and possibly spanning both at the top for twisting reinforcement. If you are making the frame out of 1" thick material, it probably won't matter though.
|
|