|
Post by gerifalte on Apr 6, 2008 20:11:31 GMT -5
Hello gents, I hope you had a good weekend! After putting only about 50hrs in my Jinma tiller the following disaster occurred: 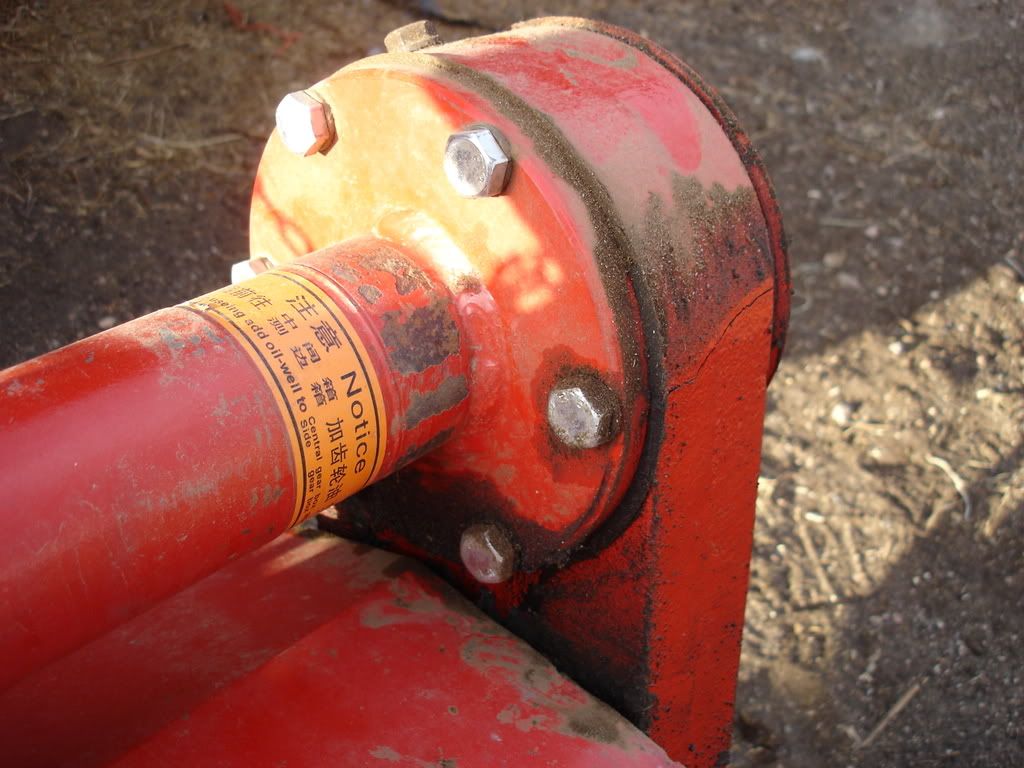 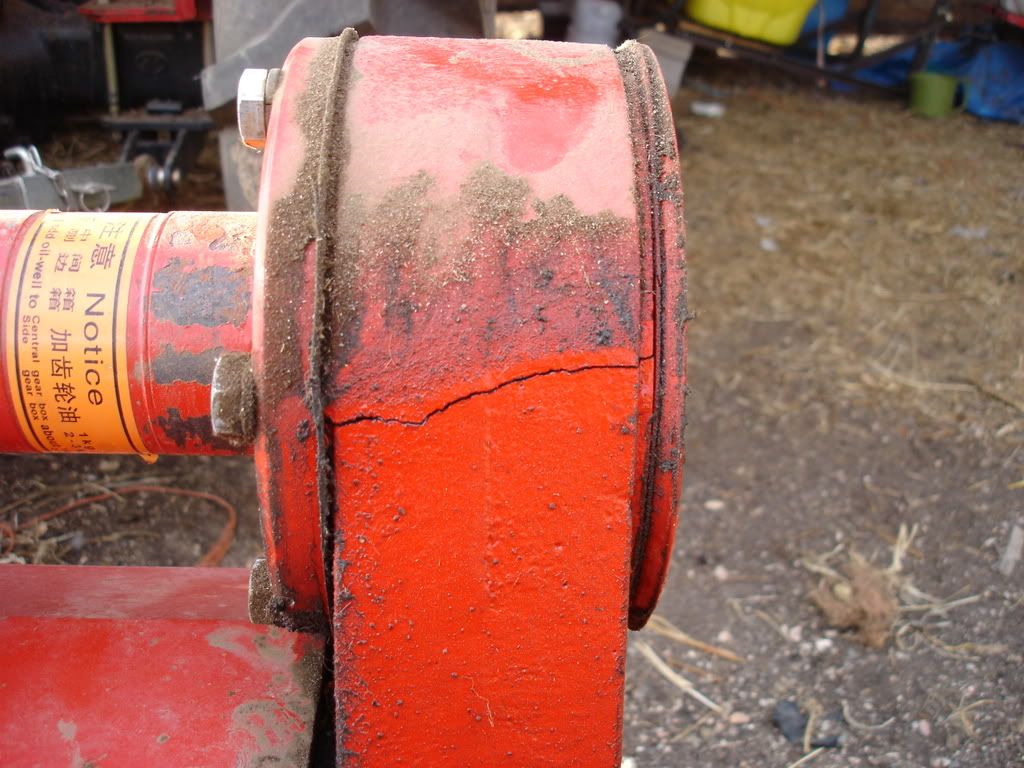 This is the cast-iron cover for the gears that run from the main shaft from the gearbox to the tiller. It is a pretty thick part (maybe 3/4 inch thick?) and because of this crack a lot of oil is leaking. I was wondering if you could give me some ideas for the repair. My current options are: 1. Repair it myself: I have taken this piece apart before and it is not a lot of work. I was thinking that I could make a bevel in the crack, and then stick weld it with several passes using a 6011 rod. Now, I have never welded cast iron so I feel a bit scared about this part. I have seen some of you have done this before to steering components and 3-ph lift arms, so I was wondering if you can give me some advice. I have a Lincoln AC/DC welder with max output of 225 amps, and also an oxy/acetylene torch. I would rather use the stick welder since I am more comfortable with that process. 2. Take the part to a professional welder (probably around $80-$100 but I am not sure). I am leaning towards this option since I have no experience welding cast iron and I want to make sure this doesn't break again. Any suggestions/tips? We need to use this implement quite a bit in the farm right now, so I want to make sure I do this right. Thanks a bunch guys! G
|
|
FlyHiFlyLo
Administrator
2007 Jinma 554LE
Posts: 425
|
Post by FlyHiFlyLo on Apr 6, 2008 21:51:41 GMT -5
One thing I would do after having it Tig welded and well peened? Add a gusset with some plug welds. 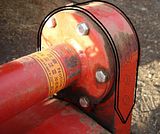
|
|
|
Post by gerifalte on Apr 6, 2008 23:16:06 GMT -5
One thing I would do after having it Tig welded and well pinged? Add a gusset with some plug welds. That's a very good idea Fly! Thanks for the tip. Can you give me any tips to weld the plugs into the cast iron? i.e. how do I preheat the iron? Would heating it up with a rosebud do? Does the 6011 rod make sense? Thanks again for your advice G
|
|
|
Post by bradblazer on Apr 6, 2008 23:32:41 GMT -5
There are special rods for welding cast iron. I think most have a high nickel content. I have heard that Stainless rod can be okay since it has a high nickel content. HF sells something called Sharpcast. Since the piece is pretty big a weed burner torch migh work well to heat it up. Check here for tips on how to do it: weldingweb.com/
|
|
FlyHiFlyLo
Administrator
2007 Jinma 554LE
Posts: 425
|
Post by FlyHiFlyLo on Apr 6, 2008 23:43:24 GMT -5
Just grind the hell out of the casting where you would be welding. In the gusset drill some 1/2-3/4" holes. Then when the gusset is welded in place on each end run the drill bit into the cast iron just enough to get the tip of the drill bit submerged into the iron. Then start your weld from the center out. Make a good puddle half way then peen it. Heat it up again and make a second weld puddle until it is flush with your gusset.
Don't use 6011, use 7018 on that crappy iron. When you peen it hit it gently. You can use nickel rod but it's spendy. The secret is the peen. When you weld it get the iron almost orange and gently pen it while it cools for several minutes. You can even bury it a foot deep in dry sand.
|
|
|
Post by gerifalte on Apr 7, 2008 0:20:23 GMT -5
Thanks a lot for your advice Brad and Fly! Much appreciated. Brad, thanks for the idea of the weed burner. I have one but I thought propane might not get it as hot as needed, whether Acetylene may do better. Your link is a great resource! In fact, I found this very useful thread about welding cast iron parts from a tractor weldingweb.com/showthread.php?t=20244&highlight=cast+ironFly, I will definitively follow your tip about peening. Do you use a ball hammer, or just about any hammer will do? Thanks again! G
|
|
FlyHiFlyLo
Administrator
2007 Jinma 554LE
Posts: 425
|
Post by FlyHiFlyLo on Apr 7, 2008 10:07:09 GMT -5
There ain't no propane torch that will get the Iron hot enough to weld. You must use O/A with a rose bud. When peening use the pointed tip of a slag hammer.
|
|
|
Post by gerifalte on Apr 7, 2008 10:36:33 GMT -5
When peening use the pointed tip of a slag hammer. Thanks again Fly. That clarifies things. By the way, I posted the same question in the welding forum that Brad pointed out, and here are the answers so far weldingweb.com/showthread.php?t=20614 The more I read, the more convinced I am to take it to a welding shop and add the reinforcements myself. I don't want this darn thing to break again! G
|
|
|
Post by bradblazer on Apr 7, 2008 12:36:01 GMT -5
I was talking about pre-heating with the weedburner, no more than 900F (very dull red). The weedburner puts out lots of BTUs cheap and will heat the whole part. I saw a thread where a guy preheated his loader bucket to add hardface and he had the whole thing glowing with a weedburner under it.
|
|
FlyHiFlyLo
Administrator
2007 Jinma 554LE
Posts: 425
|
Post by FlyHiFlyLo on Apr 7, 2008 16:21:30 GMT -5
You can heat up steel with a weedburner. But cast iron is a different animal. It takes twice as much heat to get it glowing.
|
|
3RRL
Administrator
Huge Kama
Posts: 2,027
|
Post by 3RRL on Apr 7, 2008 17:43:52 GMT -5
G- That's too bad for that crack in your tiller. I read your comment in Fly's thread and yeah, I think I have the same tiller. If you are comfortable at all with the stick welder, I'd go ahead and weld it myself. Nice generous fillet, preheat and use 7018 AC or DC rod. If you have DC, it will go on a lot easier than with AC.
My question is, how did that housing crack? Rob-
|
|
|
Post by bradblazer on Apr 7, 2008 19:43:49 GMT -5
Fly man, The specific heat capacity of cast iron is about 0.13 BTU/lbm-F vs steel at 0.116. That's only a 10% difference. It has a higher conductivity and that should help it to heat more evenly. The adiabatic flame temperature of propane with air is about 3500F. The flame from my weedburner is bigger than that gearbox. I don't have first hand experience but I have a hard time believing it won't work.
G, That turned into a good thread on Welding Web.
|
|
|
Post by gerifalte on Apr 7, 2008 21:13:50 GMT -5
My question is, how did that housing crack? Rob- Hello Rob, Thanks for your advice and encouragement. As I just "confessed" in the welding forum, I think this might be my fault since I remember tightening the bolts on that tiller REALLY tight after they fell a couple of times. I don't recall breaking anything or messing up the threads, but I do have a heavy duty 1 inch wrench + I was pretty pissed at the bolts falling twice + I am fairly strong so I do think I am probably the cause of the crack Fly said your tiller is a different brand, plus you are smarter than me and will probably use a torque wrench when you assemble yours! The welder I got a quote from today (over the phone, $75-$100) said in his experience Chinese cast iron can be low grade, so that might have influenced things as well...at least I would like to think so, so I don't feel so stupid about this! ;D Yes indeed! Quite a bit of response from knowledgeable people. I will post the results in both threads. Thanks again everyone! G
|
|
FlyHiFlyLo
Administrator
2007 Jinma 554LE
Posts: 425
|
Post by FlyHiFlyLo on Apr 7, 2008 21:15:37 GMT -5
I think I have the same tiller. Rob- No, ours are different.
|
|
|
Post by gerifalte on Apr 19, 2008 19:28:26 GMT -5
Hello all, So today I finally had some time to take the tiller apart. Here is a picture of the gear system with the cover removed. This piece seems to be intact and I couldn't see any uneven wear on the gears, so that's good news 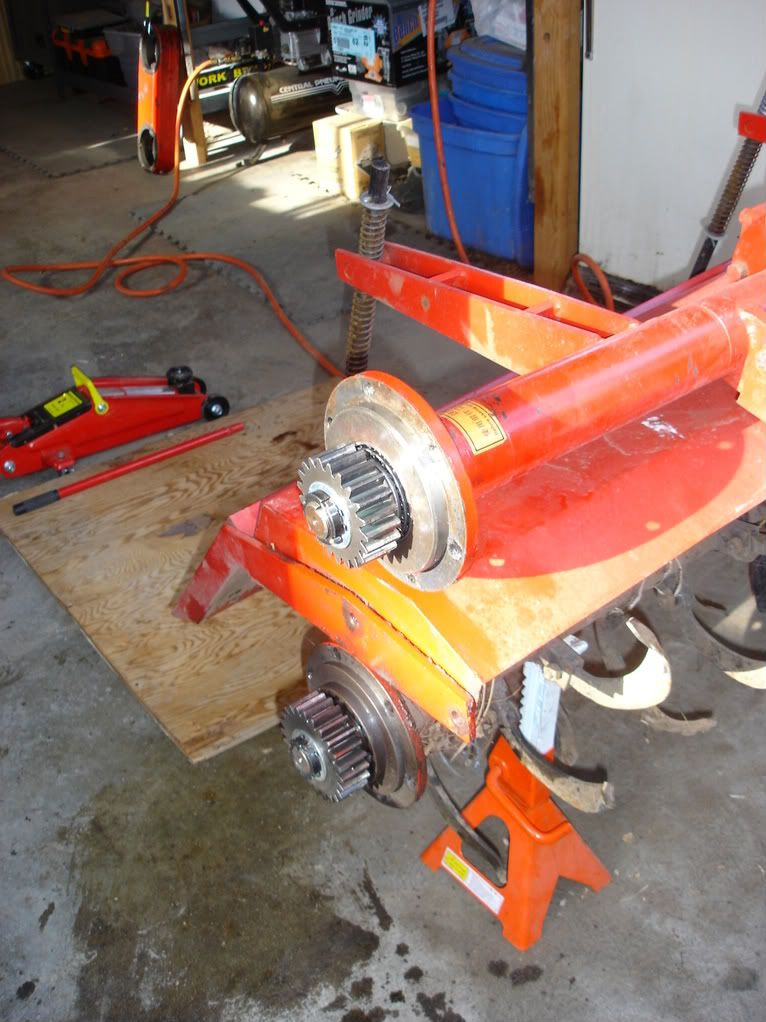 The following 2 pics show how the crack goes from side to side, and you can also see a piece of cast iron that came apart from one of the threads (piece in the bottom of the first pic). That is evidently the point where the crack started! There is also another thread pretty messed up 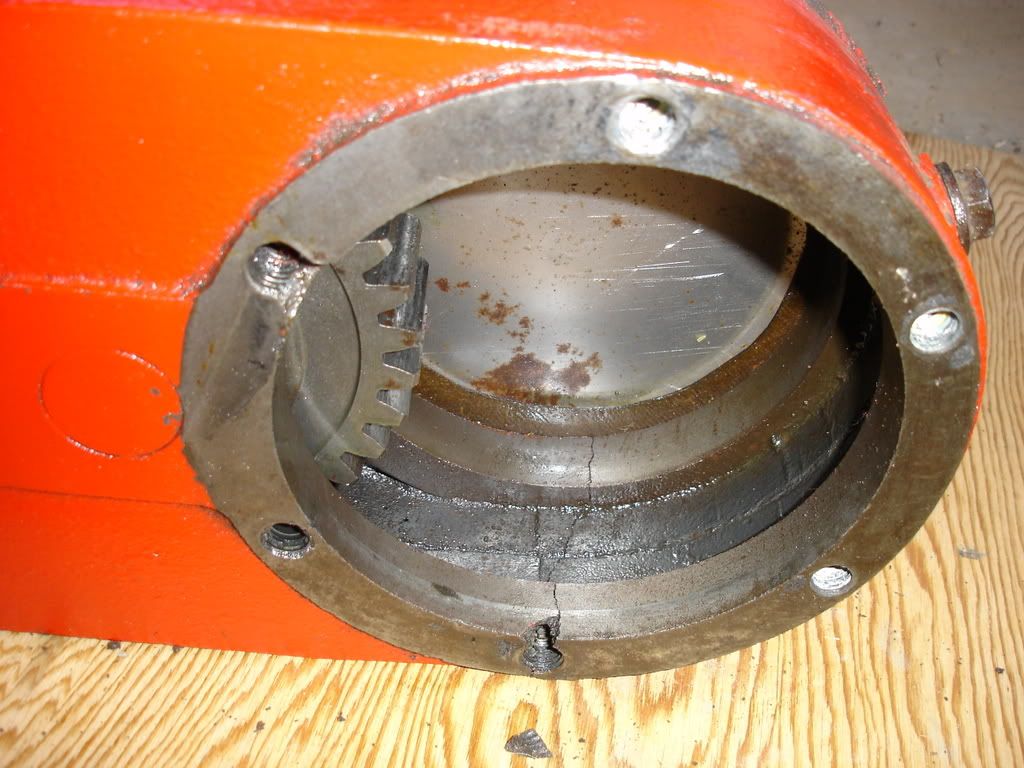 This one shows the piece after removing a protective plate and gaskets. 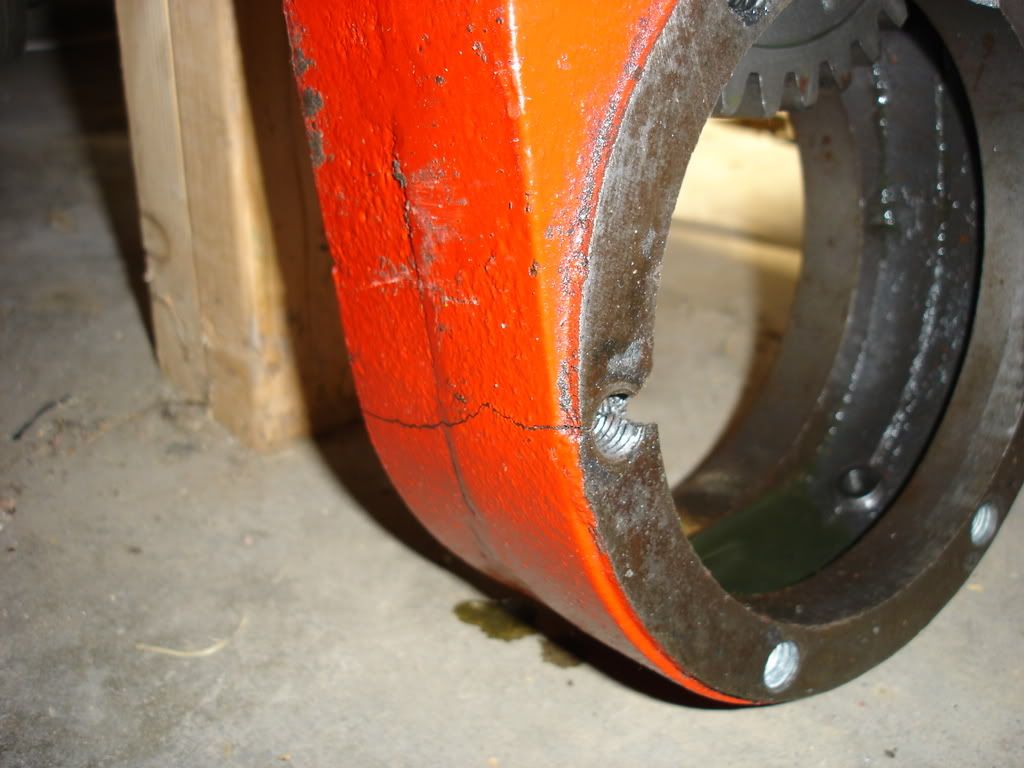 There was some water mixed with the oil  . I am guessing this was caused by the crack 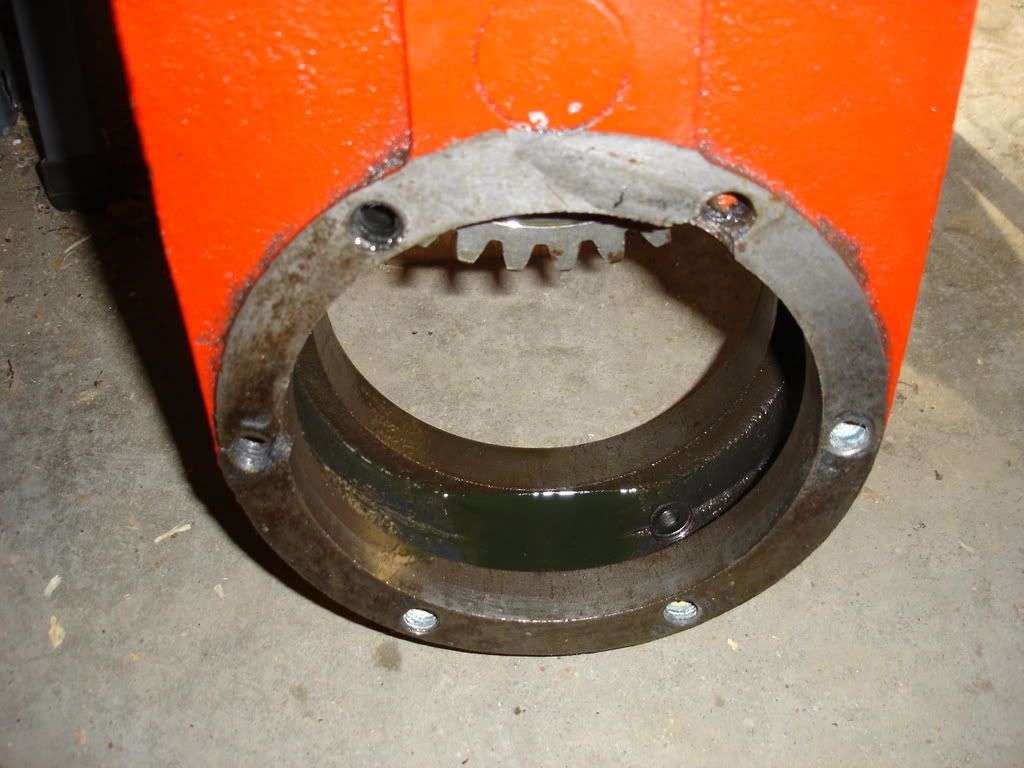 I was quoted $150 for the replacement part, and a local welder wants $75-$100 to fix it, so I figure I will give it a shot to fix it myself, and if I make a mess I can just buy the replacement part. The hardest part will be to make sure the weld in the inner circumference that connects to the main shaft is flush, so the parts will align well. I think after I weld it I will have to file it down the good'ole way with a hand file, so I don't overheat the iron. I will work on this tomorrow and will post back with the results (that is, if I can get it done by tomorrow!). Worst case scenario I will be $150 short, best case I will be pretty proud for fixing it!!! ;D Any suggestions before I take on this? To be continued....
|
|